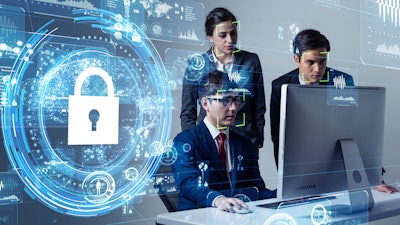
I recently sat down with Jon Meyer from Travelers, a leading provider of risk management services and insurance offerings, to discuss how advanced manufacturing technologies are impacting operations throughout the industrial sector. In addition to improving production capabilities and quality controls, all these connections and data sources expose users to new risks, which can impact insurance decisions.
Jeff Reinke, editorial Director: Why do you think there has been such a push to integrate technology into manufacturing?
Jon Meyer, Advanced Manufacturing Practice Lead at Travelers: Customers want speed and customization, and technology can help manufacturers meet those needs. Different solutions available today enable manufacturers to streamline complex processes, improve efficiencies and customer experiences, bring additional workplace safety advantages and increase productivity and profitability.
In fact, many manufacturers recognize that implementing technologies to help address different business challenges allows them to gain a competitive advantage, retain good employees and ensure future growth.
For example, embedded sensors can monitor machine performance and track data points that provide real-time insights into equipment health, and can alert workers when service and repairs are needed. Sensors, along with location-aware technology, can also assist manufacturers in the tracking of parts and supplies, allowing for real-time delivery status.
JR: Do you think the CHIPS and Science Act of 2022 impacted the advancement of technology in the industry?
JM: The CHIPS and Science Act is one of a few pieces of legislation passed in the last couple of years to help with manufacturing growth in the U.S. This act is focused on boosting the country’s competitiveness, innovation and national security through investments to create semiconductors domestically. There’s also the Inflation Reduction Act and the Bipartisan Infrastructure Law. All these projects will take years to implement, with funding continuing for the next eight years, so the pipeline looks promising now and into the future.
With many sizeable infrastructure projects in the works or anticipated as a result, manufacturers of all sizes will likely see more opportunities, whether through involvement in these initiatives themselves or because of the increased demand for manufacturing overall.
This funding could also help increase the integration of technology into the products being produced, the level of sophistication of techniques used during the manufacturing process and the advancement of industrial machinery and equipment.
That said, it’s still a marathon versus a sprint as manufacturers increasingly look to new technologies to help boost production, improve quality and reduce costs.
JR: As more manufacturers integrate technology into the workplace, what are some of the biggest risks?
JM: Cyberattacks, business interruption, workplace safety, manufacturing defects and property damage.
Starting with cyber risks, any time you connect to the internet, you’re introducing a potential entry point for a cybercriminal to exploit. Successful attacks can sabotage production, corrupt data, steal intellectual property, damage equipment and cause significant financial and reputational harm.
While a cyberattack could result in a temporary shutdown, there are other ways manufacturers could suffer significant downtime, including because of a system problem, natural disaster or other widespread event such as a fire or storm. Any shutdown can have a ripple effect on the larger supply chain, magnifying the extent of disruption and financial loss.
Technology on factory floors could also present workplace safety risks. For instance, adding robots to the production process exposes employees to moving machinery and robotic parts.
Other risks beyond workforce safety emerge with the convergence of automated and manual work. If a digital device is incorrectly integrated into plant operations – due to problems in planning or programming, for example – it could damage the facility, raw materials or finished goods. Control systems for machinery, pressurized processes or temperature-controlled environments might cause overheating, an explosion or product spoilage.
The introduction of new technology and manufacturing methods can also result in unintended product defects. The products could then fail to meet customer expectations or cause property damage, injury or financial loss, which in turn could lead to lawsuits and potentially impact the manufacturer’s brand and reputation.
JR: What role do you see insurers playing in helping manufacturers adopt technology and mitigate risks?
JM: At Travelers, we spend a considerable amount of time understanding the risks and rewards of connecting technology, people and data. When it comes to helping our customers as they consider technology investments, we take a test-and-learn approach. We explore and evaluate how different technologies work in the real world, identifying benefits and potential concerns, and then we share what we’ve learned with our customers so they can make more informed decisions.
No solution is one-size-fits-all, and we encourage our customers to test solutions themselves before investing fully to identify the right solution for their needs.
More broadly, when it comes to mitigating risks, our manufacturing customers benefit from our Risk Control department – one of the largest in the industry. Our Risk Control professionals who work with manufacturers have deep industry-specific expertise and understand the unique challenges businesses in this sector face. Along with on-site and virtual consultations, Travelers Risk Control provides tools, trainings and resources designed to help our customers manage risk.